Loch Lomond Distillery can trace its roots back over 200 years. Today, it crafts three distinctive whisky styles including its flagship Scotch single malt brand Loch Lomond Whiskies; its single grain whisky, Spearhead made from 100% malted barley and distilled in a copper coffey still; and its latest creation Noble Rebel, a range of blended malt Scotch whiskies that seek to break the norm by combining new ideas with deep-rooted traditions in whisky making. Launched in February 2023, in just a few months it has been an extraordinary success in the UK.
Recognition for Loch Lomond Whiskies came by being voted Most Awarded Distillery at San Francisco World Spirits Competition in 2023 followed by another two awards before the end of the year.
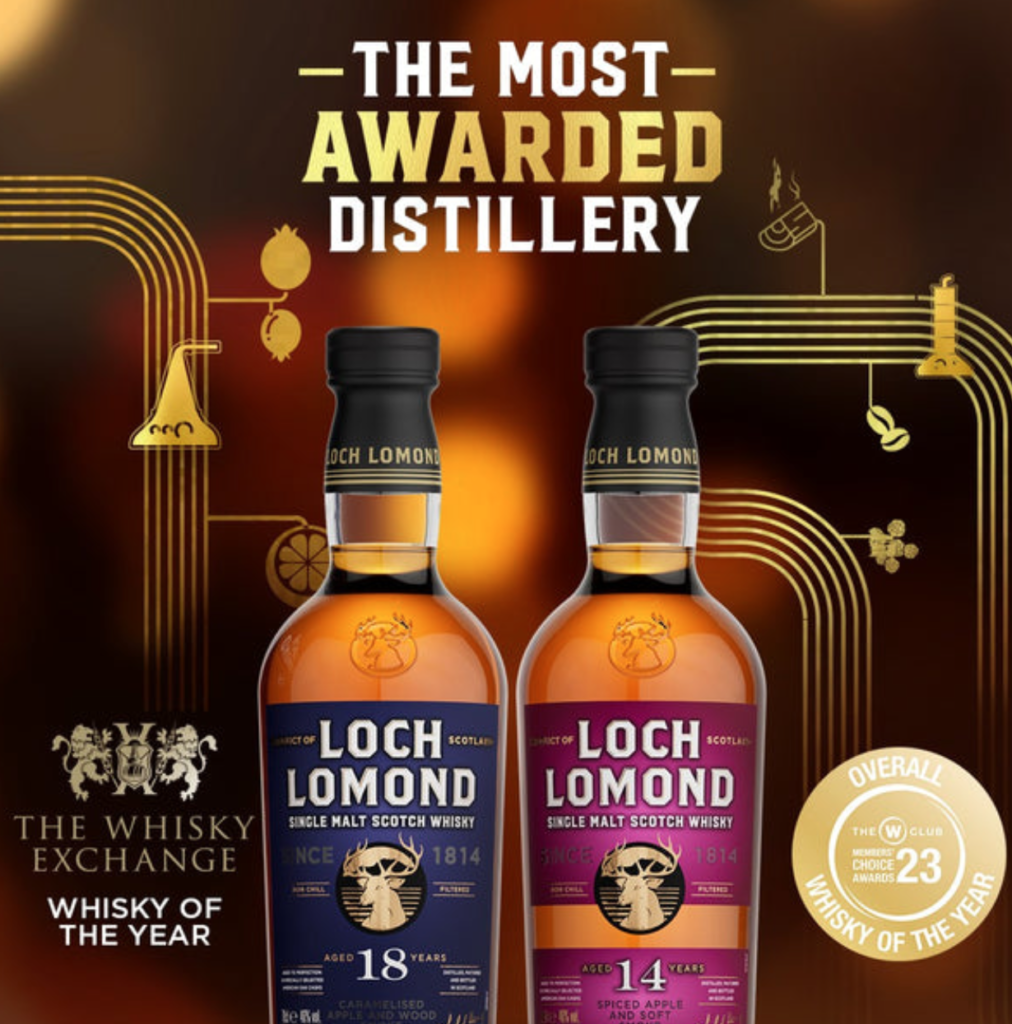
Following a rigorous voting process including several blind tastings, the Loch Lomond 18 Year Old has been named The Whisky Exchange’s Whisky of the Year! It saw off stiff competition to be voted number one by a combination of both drinks-industry experts and members of the public.
New line 4
With such a wide range of products Enterprise Tondelli were delighted when they were awarded the contract to supply the heart of line 4 with a new blower/filler/capper and infeed conveyors to provide probably the most flexible medium speed line ever!
Enterprise Tondelli have been working at the bottling plant of Loch Lomond since 2004 and have supplied much of the equipment on site ranging from high speed flask and cylindrical bottle filling to depalletising, shrink wrapping, palletising, conveying and labelling,.
This new project has a bottle filler that can handle from 500 ml PET bottles up to 1.75 litre glass jugs along with square, cylindrical and rectangular bottles all on the same line. Additionally the line can handle 11 different closures that are automatically applied. These include 8 different sizes of “T” shaped corks and 3 different sizes of ROPP caps.
The new line is located in bottling hall two which is where the shorter runs are carried out. The area is quite compact and line 4 shares the hall with the miniature line that Enterprise installed a couple of years ago.
Quick change over conveyors
Due to the variety of bottles sizes etc to be handled a bulk bottle reception mattress table was supplied that can accommodate 2 layers of bottles allowing greater autonomy in the semi-automatic depalletizing process. This was supplied by Eurosistemi who are the conveyor manufacturing partner to Enterprise. Depalletised bottles are single lined by a pressure less combiner which has the capability for many different programmes depending on the bottle. This handles both cylindrical and some of the shaped bottles.
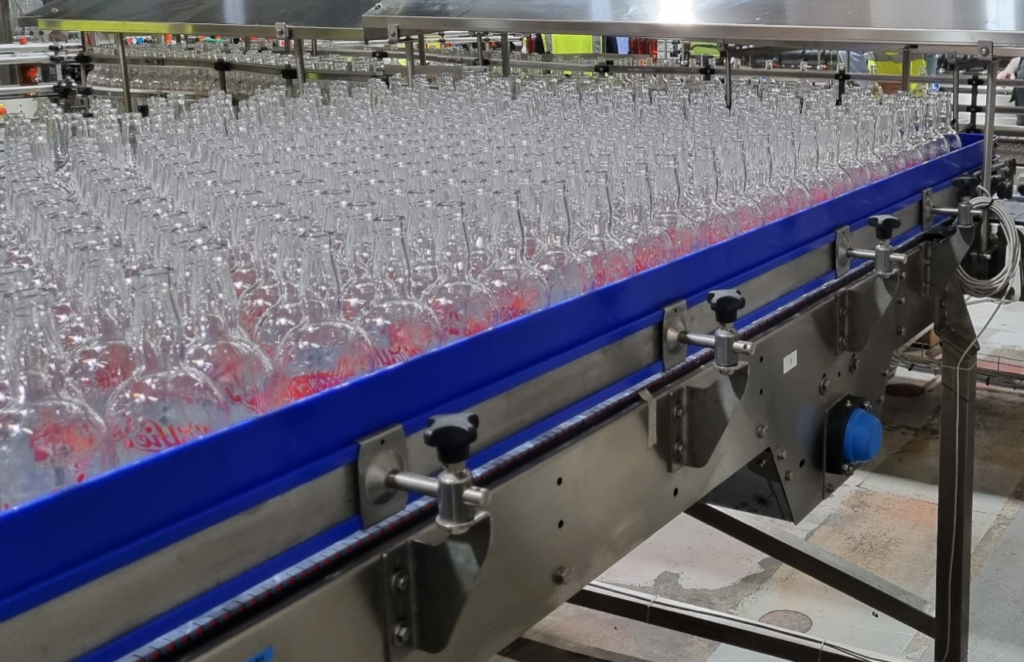
As already mentioned the area is quite compact so special disc type bends where used with quick change over system to accommodate the very differing bottle sizes using quick adjustment levers. No change parts are required thus allow quicker size changes. The conveyors are controlled from the Eurosistemi stainless steel panel which has a touch screen hmi for menu selection. The software is open allows the customer to add new programmes for any future bottles that may arise.
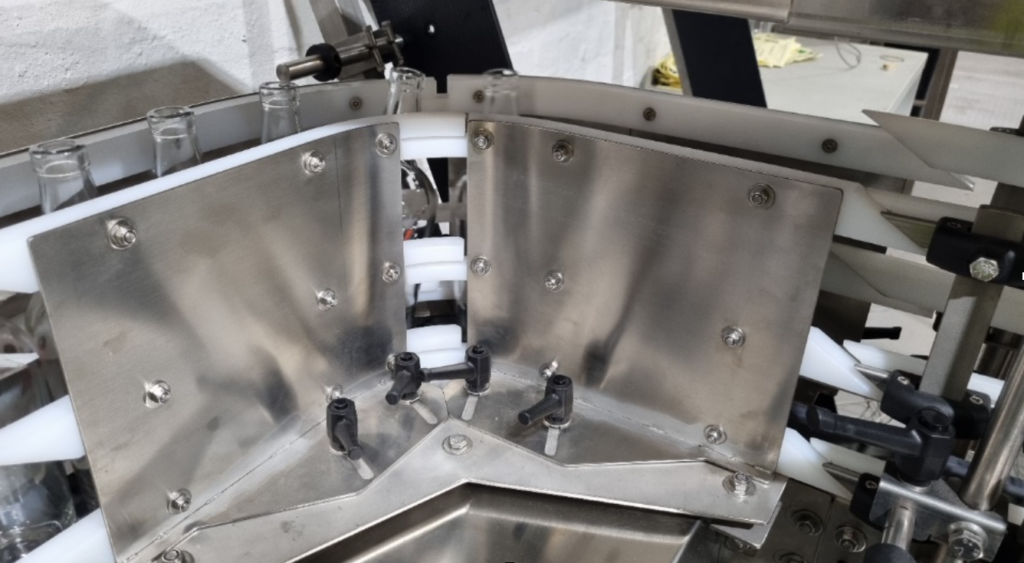
Adjustable change parts blower/filler/capper
The bottles are fed to a monobloc blower/filler/capper which has a number of interesting features. With 28 bottles the traditional change parts would have consisted of at least 11 different components including starwheels, wormscrew etc. However Enterprise supplied an adjustable starwheels system and universal wormscrew that allows most of the bottles to be handled with no bottle handling change parts at all except the rinser grippers.
Fill level on the low vacuum filler is set from the operator panel and each bottle has its own pre-set value for repeatability. Two stage air filtration was fitted for the rotary bottle cleaner along with low air pressure alarm and also missing cork detection on the discharge to ensure product integrity.
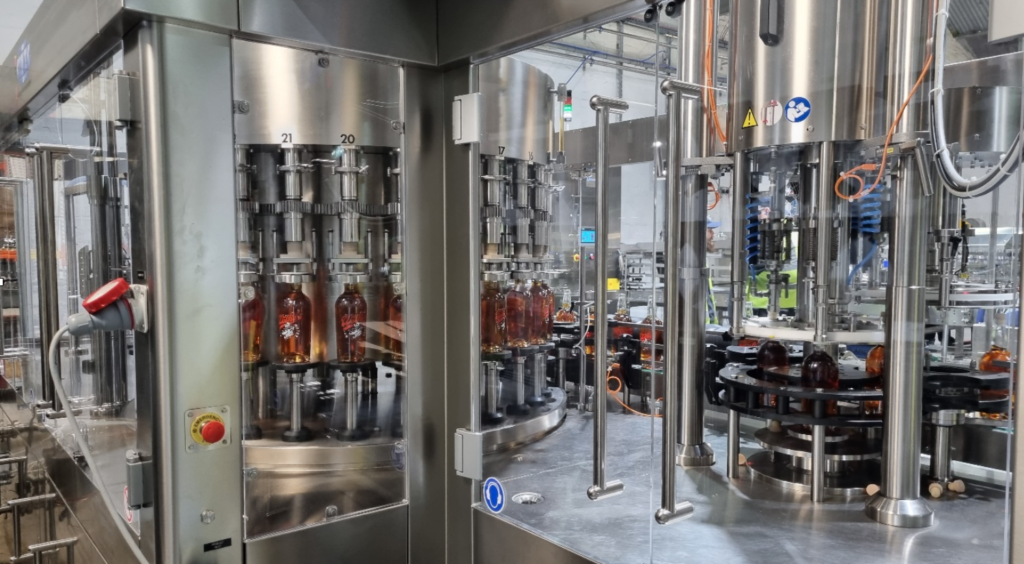
A modem is fitted in the panel for remote assistance. A low level cap hopper and flited belt elevator feeding the dual purpose capping turret ensures safe working for the operators. A pre-set bottle count er allows them to set how many bottles to produce before the filler stops and advises batch complete so just the number of bottles are filled with no manual counting.
The conveyor layout produced in the UK office of Enterprise Tondelli also meant that one operator was centrally located to monitor several aspects of the line reducing wasted movement.
The machine will fill both brown and white spirits as well as some new ranges of products such as flavoured liquors. To ensure good hygiene CIP cups were also supplied to allowing machine cleaning without medium going to waste or creating a slip hazard on the floor.
Craig Wilson Managing Director of Enterprise Tondelli stated: “We have had the privilege of working at Loch Lomond for many many years now and appreciate the confidence that Loch Lomond have invested in Enterprise. Their professionalism and understanding of their requirements make them a joy to work with and we look forward to continuing to be able to assist them in the future”.
Stop Press
Another two bottle sizes are now being handled bringing the total to 30 different bottle shapes and sizes. Enterprise Tondelli have been working in the industry since 1977 and supplying equipment in over 40 countries. The Wye Valley project is just one of the latest projects by Enterprise that have ranged in scope from Kombucha bottling, nitro beer canning and turn key beer bottling. Suppling canning lines 1,500 to 72,000 cans per hour , bottling from 600 to 60,000 bph and kegging lines too. This wealth of experience ensures Enterprise add something to all their projects.”